Unlocking the Power of Welding WPS: Methods for Efficiency and Safety And Security in Fabrication
In the realm of manufacture, Welding Treatment Requirements (WPS) stand as the foundation of welding operations, dictating the needed steps for achieving both efficiency and safety in the construction process. Comprehending the details of WPS is paramount to utilizing its complete potential, yet several companies struggle to unlock the real power that lies within these papers (welding WPS). By delving into the approaches that optimize welding WPS, a globe of improved performance and increased security waits for those going to discover the nuances of this vital aspect of manufacture

Value of Welding WPS
The value of Welding Treatment Specs (WPS) in the manufacture sector can not be overstated. WPS work as a crucial roadmap that lays out the needed steps to make certain welds are executed regularly and appropriately. By defining important parameters such as welding processes, materials, joint designs, preheat temperatures, interpass temperature levels, filler metals, and post-weld heat treatment demands, WPS provide a standardized method to welding that enhances efficiency, quality, and safety in manufacture processes.
Adherence to WPS helps in accomplishing uniformity in weld quality, reducing the probability of defects or architectural failures. This standardization likewise facilitates compliance with market regulations and codes, making sure that made frameworks satisfy the needed safety and security criteria. Furthermore, WPS paperwork allows welders to reproduce successful welding procedures, bring about consistent results across various projects.
Fundamentally, the meticulous growth and stringent adherence to Welding Treatment Specifications are critical for supporting the integrity of welded frameworks, protecting versus potential threats, and maintaining the credibility of fabrication business for supplying top notch items and services.
Key Aspects of Welding WPS
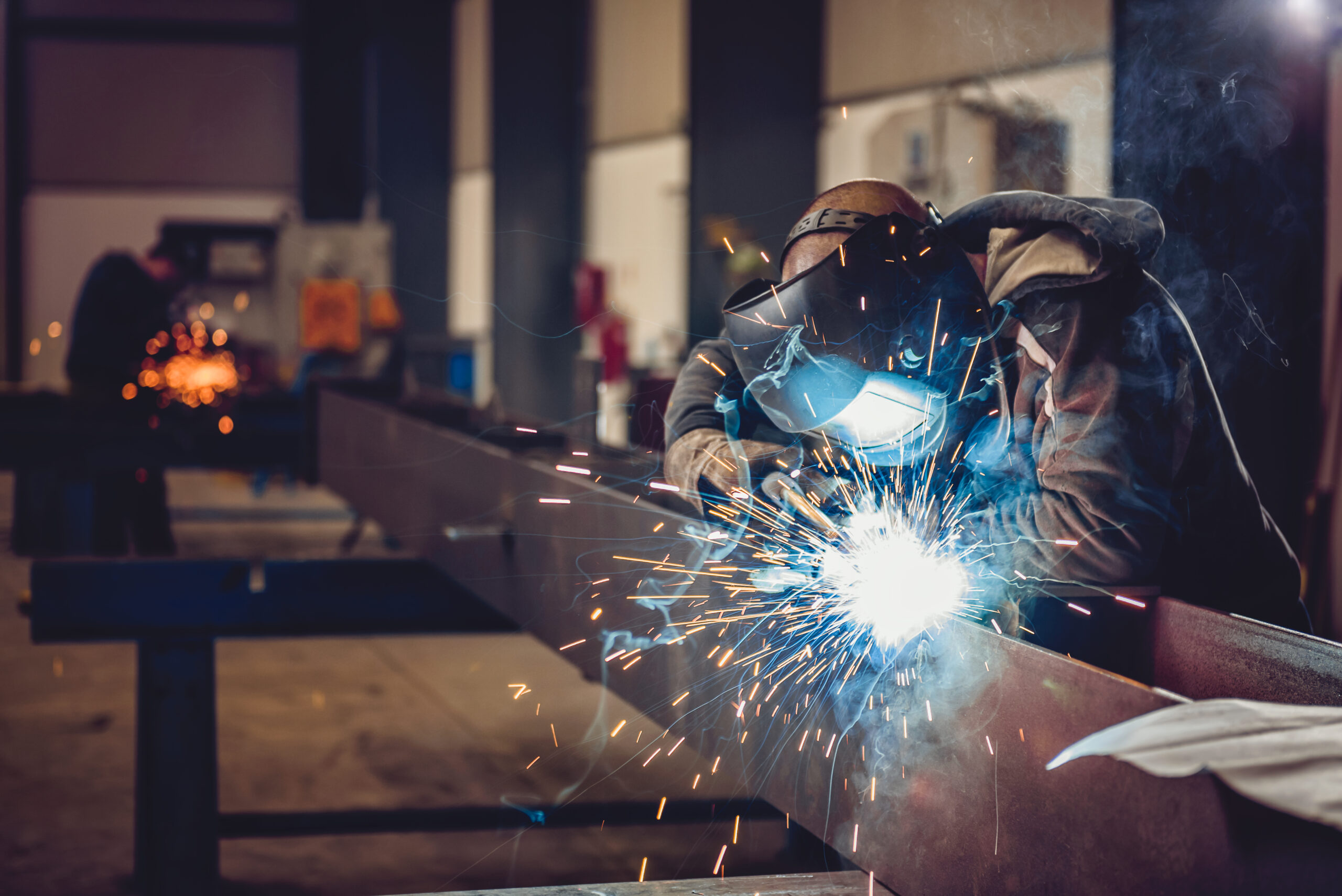
Enhancing Performance With WPS
When optimizing welding procedures, leveraging the vital aspects described in this post Welding Procedure Specifications (WPS) becomes necessary for improving procedures and making the most of productivity. One way to enhance effectiveness with WPS is by very carefully selecting the ideal welding criteria. By adhering to the certain standards supplied in the WPS, welders can ensure that the welding equipment is established appropriately, resulting in consistent and high-quality welds. Furthermore, adhering to the pre-approved welding sequences detailed in the WPS can significantly decrease the moment invested on each weld, inevitably enhancing total efficiency.
Routinely examining and updating the WPS to include any lessons found out or technological innovations can also contribute to efficiency enhancements in welding procedures. By accepting the standards established forth in the WPS and constantly seeking means to enhance procedures, fabricators can accomplish higher performance levels and premium end outcomes.
Ensuring Security in Manufacture
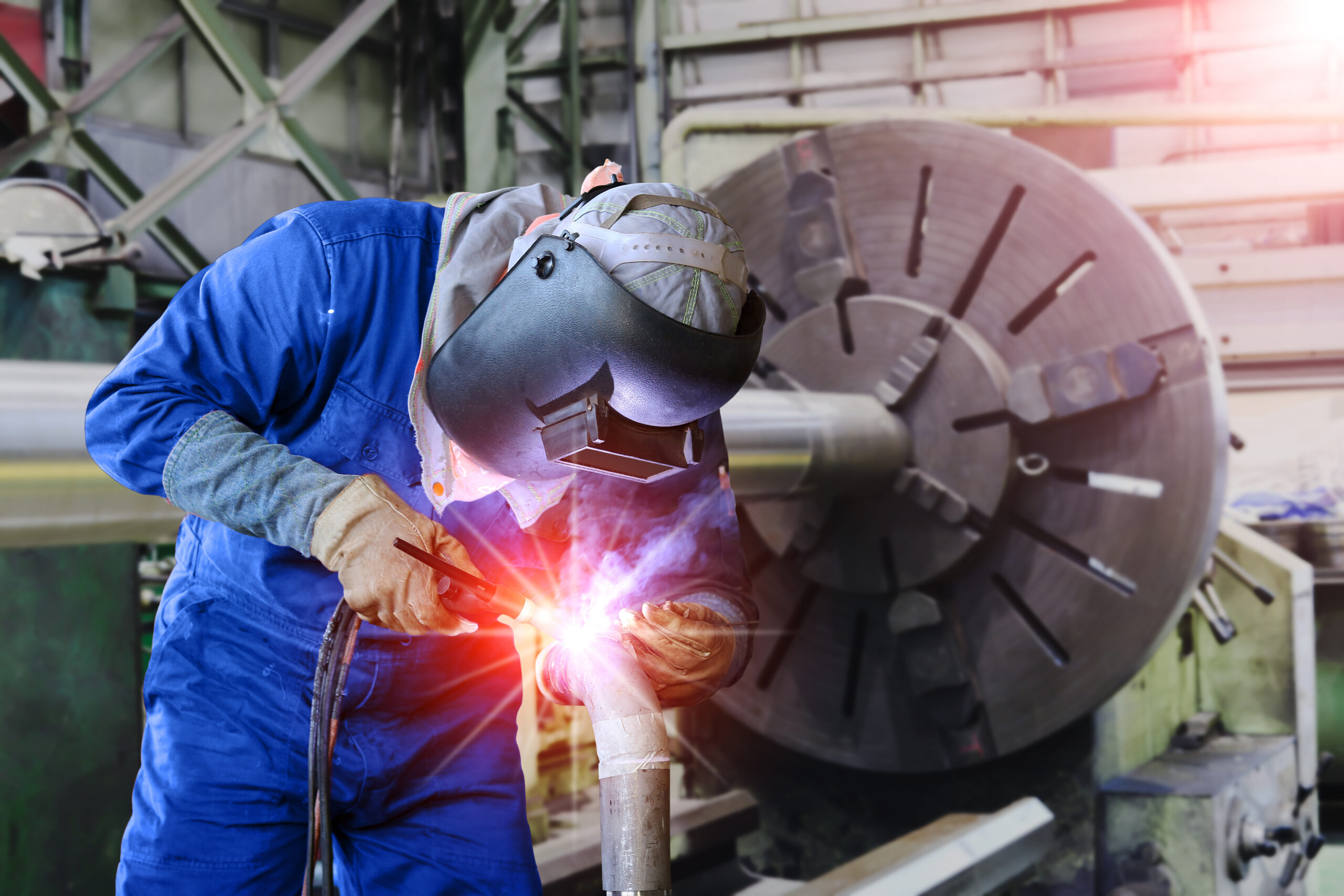
Safety methods in manufacture play a pivotal duty in guarding workers and optimizing functional procedures. Making sure safety and security in manufacture entails a multifaceted technique that includes numerous elements of the welding procedure. One basic aspect is the arrangement of individual protective devices (PPE) customized to the certain dangers existing in the construction setting. Welders must be equipped with suitable gear such as helmets, gloves, and safety apparel to reduce risks associated with welding tasks.
Additionally, adherence to correct ventilation and fume removal systems is essential in preserving a healthy and balanced job environment. Welding fumes consist of damaging compounds that, if breathed in, can position serious wellness risks. Carrying out efficient air flow steps helps to lessen exposure to these dangerous fumes, promoting respiratory system health amongst employees.
Regular equipment maintenance and evaluations are likewise useful content vital for making certain safety and security in fabrication. Defective machinery can cause mishaps and injuries, emphasizing the importance of regular checks and prompt fixings. By focusing on safety and security steps and promoting a culture of recognition, manufacture centers can produce a efficient and safe and secure work setting for their personnel.
Executing WPS Ideal Practices
To enhance operational performance and make sure high quality end results in fabrication procedures, including Welding Treatment Spec (WPS) ideal techniques is extremely important. Choosing the suitable welding process, filler product, and preheat temperature level specified in the WPS is crucial for accomplishing the wanted weld top quality. Making certain that certified welders with the necessary accreditations lug out the welding procedures according to the WPS standards is crucial for uniformity and integrity.
Conclusion
In final thought, welding WPS plays a vital role in making sure effectiveness and safety and security in manufacture procedures. By following these methods, organizations can open the full potential of welding WPS in their construction procedures.
In the realm of manufacture, Welding Procedure Requirements (WPS) stand as the foundation of welding operations, dictating the needed actions for attaining both performance and security in the manufacture procedure. By specifying crucial specifications such as welding procedures, products, joint styles, preheat temperature levels, interpass temperatures, filler steels, and post-weld heat therapy needs, WPS offer a standardized technique to welding that enhances effectiveness, quality, and safety in fabrication procedures.
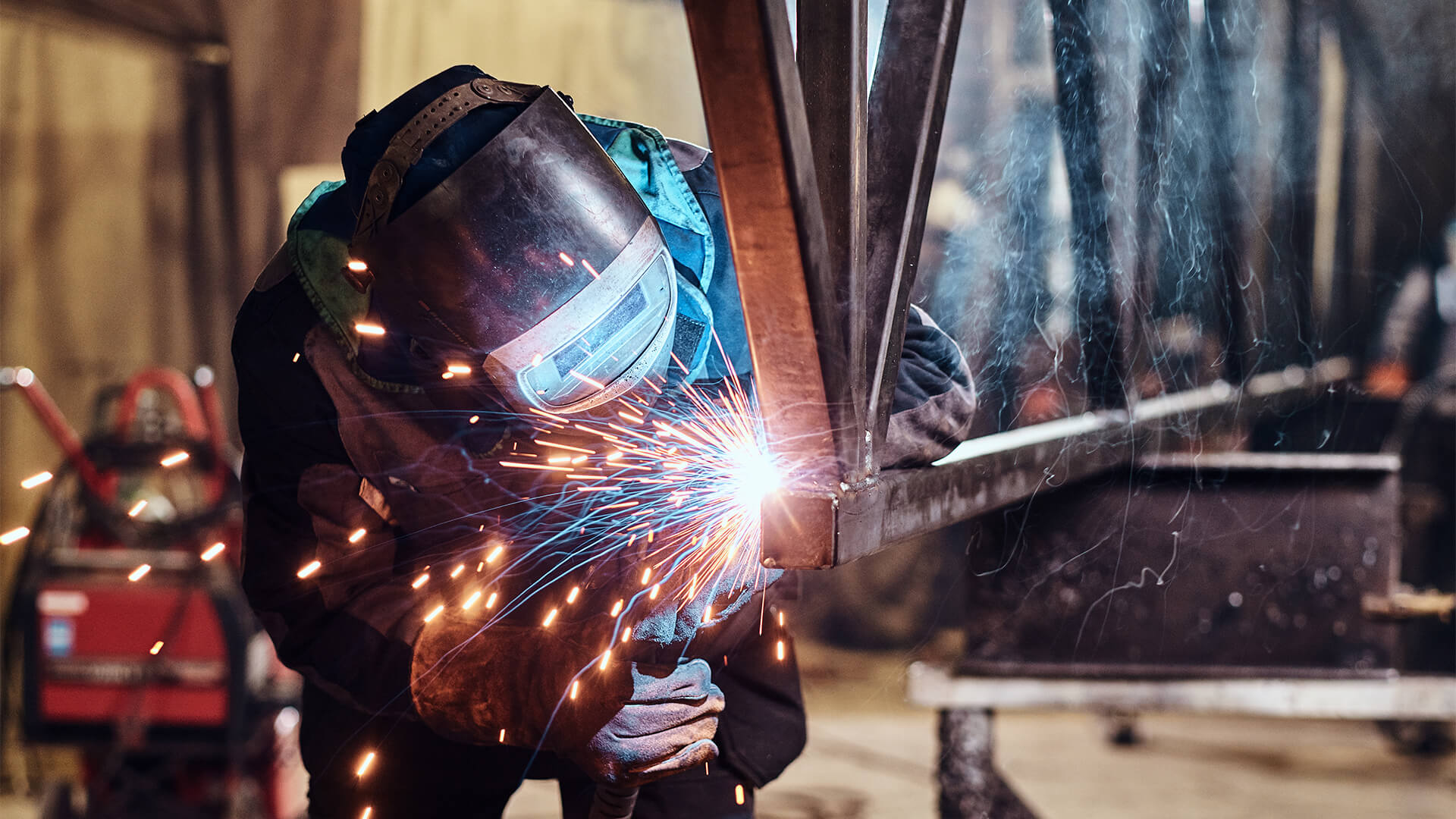
When enhancing welding procedures, leveraging the crucial aspects laid out in Welding Treatment Specs (WPS) comes to be crucial for streamlining procedures and maximizing productivity. (welding find more information WPS)